We are a family business from The Netherlands, founded in 1924. Since our foundation, we’ve held a strong belief in the power of innovation to increase the efficiency of our customers’ bulk handling operations.
About SMT Shipping case study
Our customer, SMT Shipping, has achieved significant transhipment advancements, particularly in West Africa on the TSV Conakry Pearl. This region presents a unique challenge due to its shallow shores, extending 10 to 20 meters in depth for up to 10 miles. To be profitable, you will have to ship your cargo with colossal ore carriers. These cape-size vessels can export up to 200,000 tonnes.
However, these fully loaded enormous vessels, 18 meters in depth, cannot approach the shore. The traditional solutions, like constructing extensive jetties or dredging long channels, are economically unviable. This is where SMT Shipping’s expertise comes into play.
SMT stands for innovation and integrity globally, with a 1700-strong global workforce and offices in Poland, Cyprus, the US, the UK, and the Netherlands. Marc Smeets has been working here as a Technical Project Manager for six years, and he’s now working on a transship ping project in Sierra Leone. This global maritime group of companies is involved in the shipping and transhipment of dry bulk cargo. Over the years of expansion, they entered into Joint Ventures, acquiring vessels to optimise their customers’ cargo operations and adding new ships to their approximately 62-vessel fleet.
SMT has four service divisions:
• bulk carriers and general cargo carriers
• transhipment
• cement carriers
• multi-purpose carriers
Renowned for transporting dry bulk from all kinds of ore and grain to scrap and salt, they have built their reputation as a trusted tonnage provider and business partner in the dry bulk market. Their cargo clients include mines, raw material end-users, traders, importers and exporters.
The challenge - the search for the optimal crane and grab combination
Originally, SMT’s vessels in West Africa transferred bauxite. When the bauxite market collapsed, SMT was compelled to shift to iron ore transfer for a client in Sierra Leone. This transition posed challenges due to the differing specific gravities of bauxite and iron ore.
Bauxite is lighter than iron ore, respectively around 1.6 versus 2.5 tonnes per cubic meter. Therefore, each material asks for a unique type of grab that maximizes efficiency without compromising the safety and integrity of the crane system.
The solution - enabling a higher efficiency rate witht the nemax grab
The NemaX grab stood out because of its efficiency. Traditional clamshell grabs require a significant amount of wire to be pulled in and out, taking valuable time with each cycle. In contrast, the NemaX grab uses a fraction of the wire length compared to standard grabs. In the case of SMT’s small clamshell grab, the wire length is 13,0 meters compared to the 8,7 meters of the NemaX grab.
The results - a 25% increased productivity, three months ROI and easier maintenance
Following the integration of the NemaX grab into SMT Shipping’s operations, the company witnessed a remarkable surge in productivity. The crew had to get used to the new grab in the first weeks.
But after their first month, the handling rate went from 1000 to 1250 tonnes per hour. The NemaX Grab boosted productivity by 25% compared to the previous Nemag scissor grab, which wasn’t optimally suited for iron ore.
The right grab for the right job in this continuous transhipment process was an excellent decision - despite the other three available grabs at the ship. The stark improvement in performance resulted in an exceptional return on investment period of less than three months
The future plans - the next steps
After seeing the success of the NemaX grab, SMT was eager to keep improving. If you continuously rotate a 180-degree cycle in the open sea, it results in some accidental sideways collisions now and then. The skilled crew of mainly Polish workers welded some modifications. These enhanced the grab’s strength without any downtime of the grab leaving the vessel.
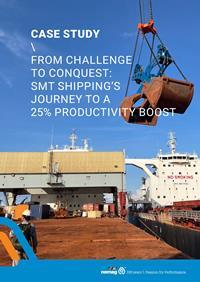
Nemag CaseStudy SMT Shipping
CASE STUDY
From Challenge To Conquest:
SMT Shipping’s Journey To A 25% Productivity Boost
DOWNLOADDo you have the right grab for the right job?
Are you ready to boost your unloading productivity, create a safer work environment, and reduce operating costs?
Nemag is here to help. Our grab specialists are happy to advise you on the best solution for your specific situation.
Request a performance calculation today - free of charge and without any obligation.
Unlock your productivity potential and schedule your free consultation with Martine: martine.dekker@nemag.com.